Sign in to follow this
Followers
0
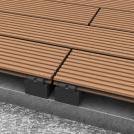
Problems To Be Solved in Wood-Plastic Materials
By
Tom Liu, in Renovation Contractors, Interior Designers & Suppliers Reviews
By
Tom Liu, in Renovation Contractors, Interior Designers & Suppliers Reviews