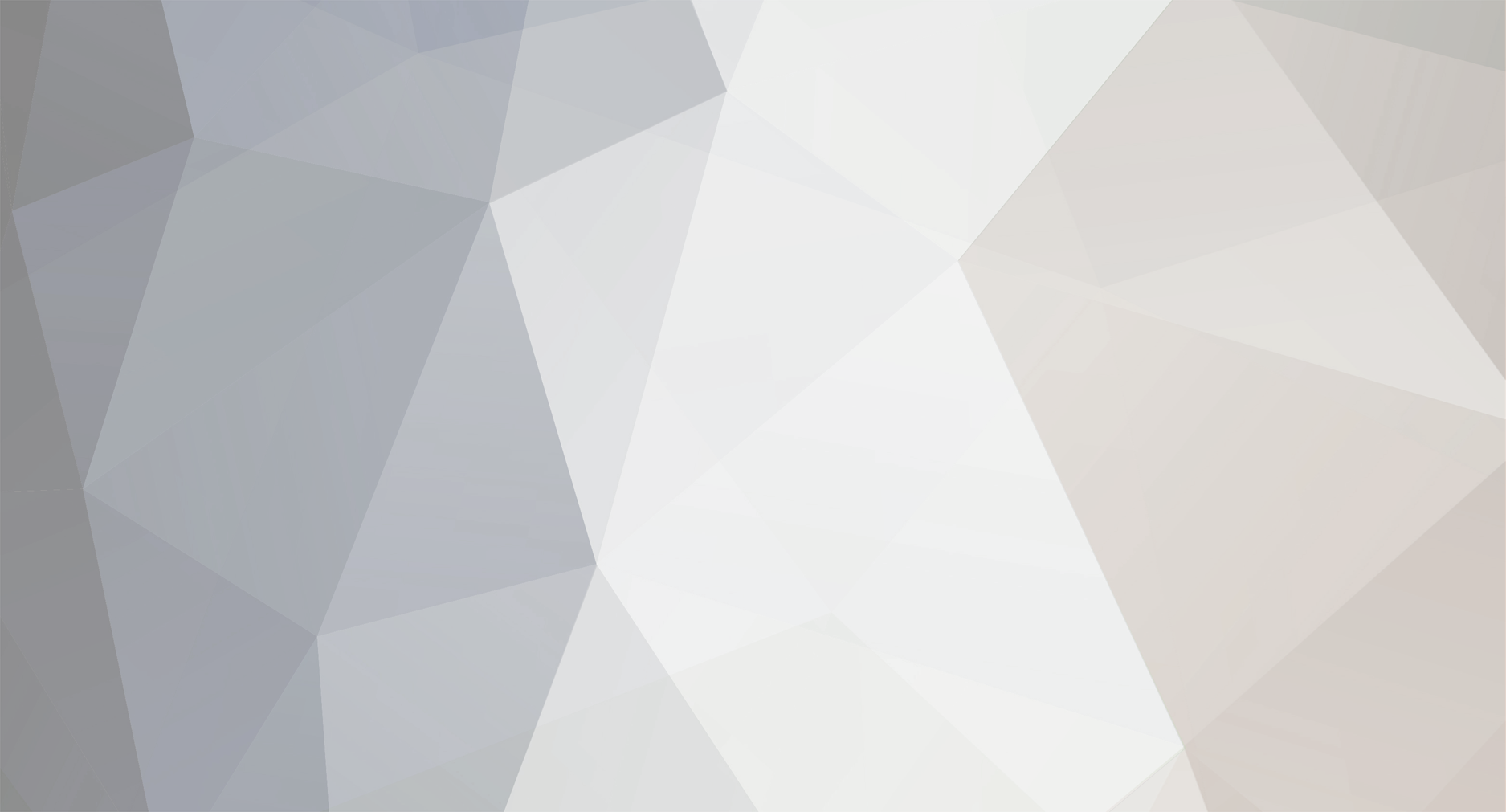
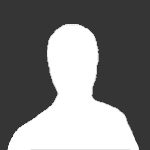
Hopersky0819
-
Content Count
5 -
Joined
-
Last visited
Single Status Update
See all updates by Hopersky0819
-
UV Curing Technologies (Part2)
Traditional UV Curing Technologies
The industrial wood finisher has essentially three options in types of UV-curable coatings to use—100% UV, water-reduced UV and solvent reduced UV. Each type of UV-curable coating can be applied by virtually any method of application. The selected method of application is dependent on a few factors, which include the surface structure/property to be finished, the finish quality desired on that surface, and the production rate that finishing must conform to. The selection of the UV-curable coating type applied by any method is really a matter of finish build or thickness, the ease to achieve certain finish subtleties (gloss, leveling, etc.), and the ease of use of the coating system. If very thin film builds are desired, less than 100% actives may be necessary and the use of water-reduced UV-curable coatings is most preferential. Water-reduced UV-curable coatings present significant advantages vs. solvent-reduced forms due to potential safety and air reporting factors.
UV lamp requirements are closely related to the formulation to be cured and its reactivity. Currently, most UV systems for flat line wood coating operations are Hg arc lamps [3]. The effectiveness of UV lamp is dependent on the type of acrylate used and their functionality. For instance, cure speed is higher for epoxy acrylate followed by polyester acrylate, urethane acrylate, and finally unsaturated polyester acrylate [4].
More recently, the use of UV-Light Emitting Diodes (UV-LEDs) have become the gold standard and have since become the ideal alternative [2] due to its many benefits over traditional broad-spectrum UV.
The introduction of UV-LED technology has led to a steady replacement of conventional mercury or gallium arc lamps. This is not surprising given the suitability of the UV-LED technology for heat-sensitive substrates, their energy efficiency, LED lifetime and its instant on/off capability, not to mention the fact that it is an environmentally friendly technology (ozone free and reduction of carbon footprint). [5].
As UV-LEDs emit energy in the form of photos, their output is one very narrow band (± 10 nm) where 96% of the energy is emitted. Thus, the wavelength of the emitted photons depends on the material used for the construction of the diode. On the other hand, conventional arc lamps gives a broad UV spectrum with several peaks distributed throughout, so they are less efficient. As UV-LEDs do not emit infrared energy, they do not contribute to heat buildup like conventional UV lamps. Moreover, since UV-LED consumes 50% less energy due to its instant on/off capability, so it has a significantly longer service life. In fact, according to literature, it is possible to achieve up to 30% energy savings [8].
These made UV-LED the ideal technology of choice for wood coating. Traditional UV technology still emit some heat which can be a problem for wood coating, since wood is a heat-sensitive material. UV-LEDs emit no infrared energy, so they are safe especially for wood products which require immediate packaging after coating [7].
This is not to say that UV-LED technology is perfect.
In fact, according to Radtech [2], usage of the technology is limited by a few factors.
(i) the lack of suitable curable materials, (ii) expensive, and (iii) sensitivity to heat which requires an additional cooling circuit.
Commercial Interior Design & Renovation Services : Renovator Hub